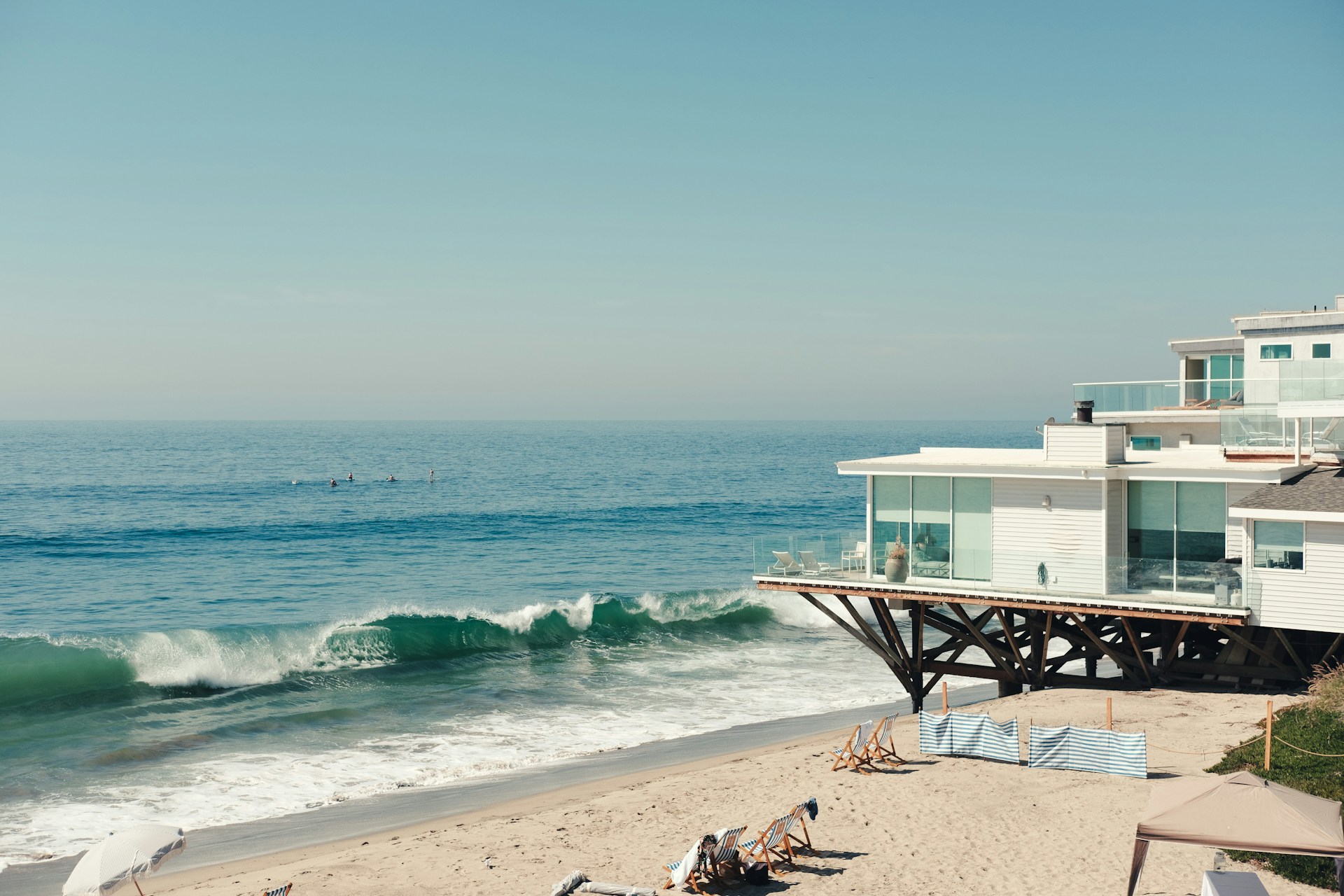
How to Maintain a Standby Generator in Coastal and Saltwater Environments
Published: December 21, 2025 | By Maria Torres, Coastal Power Systems Specialist
Standby generators in coastal environments face a uniquely harsh set of challenges. Salt-laden air, high humidity, and extreme weather events combine to create one of the most corrosive environments for mechanical and electrical equipment.
Without specialized maintenance practices, generators in coastal areas typically experience three times faster deterioration than those in inland locations. Components that might last 15-20 years elsewhere often fail within 5-7 years in saltwater environments.
This comprehensive guide outlines the specific maintenance strategies required to protect your standby generator investment in coastal settings, ensuring reliable performance when you need backup power most.
Key Takeaway: Standard generator maintenance schedules and procedures are insufficient for coastal environments. Saltwater proximity requires more frequent servicing, specialized protective coatings, upgraded components, and careful attention to corrosion prevention. With proper coastal-specific maintenance, your generator can deliver reliable service despite challenging marine conditions.
The Unique Challenges of Coastal Generator Operation
Before developing a maintenance strategy, it's essential to understand the specific threats coastal environments pose to standby generator systems:
Salt Air Corrosion
- Microscopic salt particles penetrate virtually all enclosures
- Accelerated oxidation of metal components
- Electrical connection degradation
- Corrosive attack on aluminum and steel surfaces
- Cooling system efficiency reduction
- Exhaust system deterioration
- Fastener and mounting hardware failure
High Humidity Challenges
- Constant moisture encourages rust formation
- Electrical component insulation breakdown
- Control board and circuit damage
- Fuel contamination from condensation
- Mold and microbial growth in enclosures
- Starter and alternator degradation
- Wiring harness corrosion
Extreme Weather Exposure
- Higher frequency of major storms and flooding
- Salt spray events during high winds
- Rapid temperature and humidity fluctuations
- UV degradation of components accelerated by water reflection
- Sand and saltwater intrusion during storms
- Foundation undermining from erosion
- Wind-driven debris impacts
Accelerated Wear Patterns
- Engine intake air loaded with salt particles
- Higher starting resistance due to corrosion
- Increased friction on moving parts
- Faster oil contamination rates
- Elevated cooling system deterioration
- Electrical connection resistance increases
- Battery life reduced by up to 50%
These factors combine to create an operating environment that demands specialized maintenance practices. Generators located within one mile of saltwater are particularly vulnerable, but salt air effects can extend 10+ miles inland in many coastal regions.
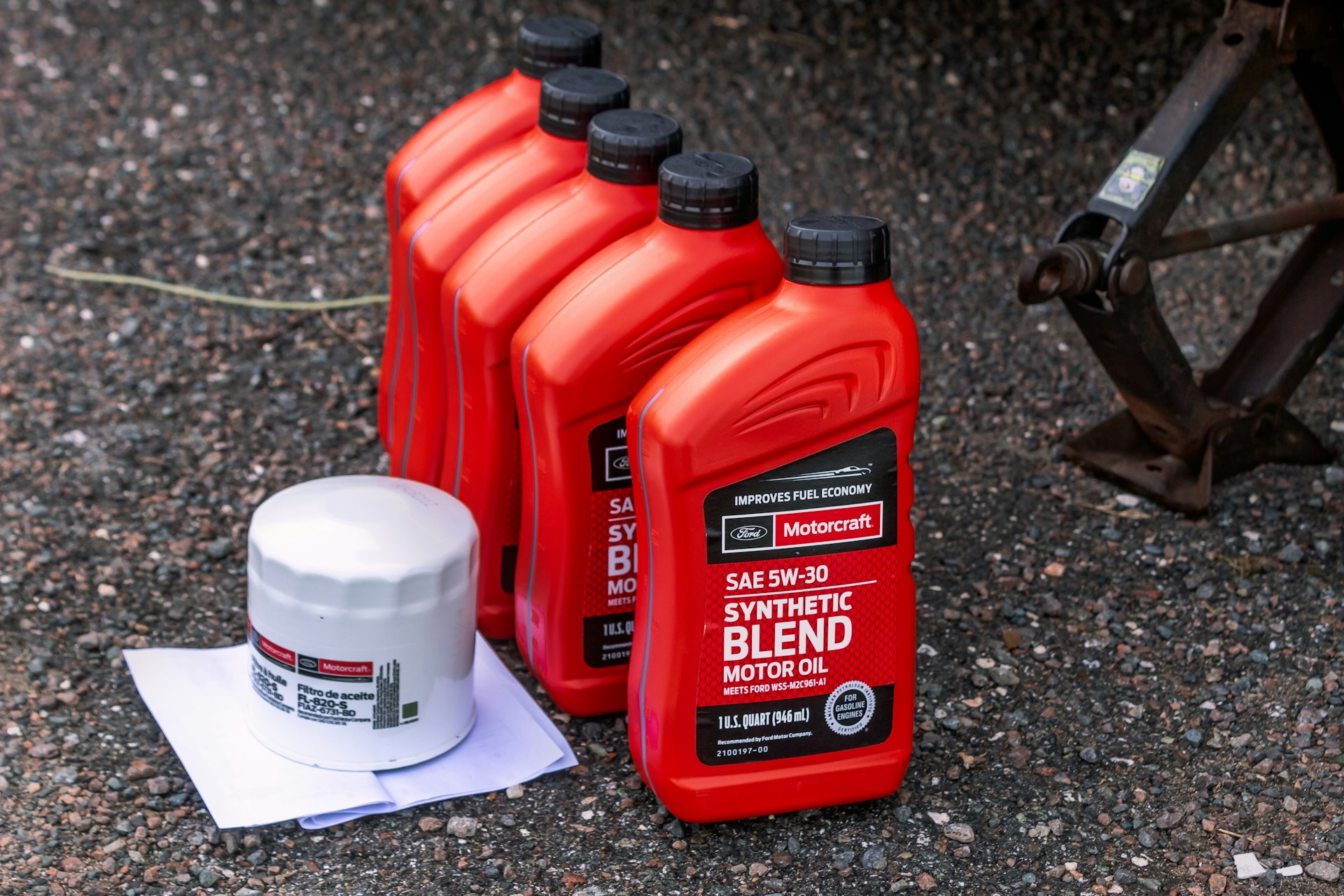
Salt air corrosion damage on a generator that lacked proper coastal maintenance
Coastal Generator Maintenance Schedule
The first adjustment needed for coastal generators is an accelerated maintenance schedule:
Maintenance Task | Standard Interval | Coastal Interval | Special Considerations |
---|---|---|---|
Visual Inspection | Monthly | Bi-weekly | Focus on early corrosion detection and salt buildup |
Oil & Filter Change | Annually or 100hrs | Every 6 months or 50hrs | Use marine-grade oil with higher detergent content |
Air Filter Replacement | Annually | Quarterly | Consider pre-filter or salt air filtration system |
Enclosure Cleaning | As needed | Monthly | Use fresh water rinse with specific techniques |
Battery Inspection | Quarterly | Monthly | Apply terminal protectants after each check |
Battery Replacement | Every 3-5 years | Every 2-3 years | Use marine-rated batteries when possible |
Electrical Connection Check | Annually | Quarterly | Apply dielectric grease to all connections |
Cooling System Service | Every 2 years | Annually | Use corrosion-inhibiting coolant formulations |
Fuel System Treatment | As needed | Quarterly | Add moisture-control fuel additives regularly |
Protective Coating Renewal | Not typically required | Annually | Apply marine-grade protectants to susceptible surfaces |
Full Professional Service | Annually | Every 6 months | Use technicians experienced with coastal generators |
This accelerated schedule represents the minimum recommended maintenance frequency for generators within one mile of saltwater. Systems directly exposed to salt spray or in severe coastal environments may require even more frequent attention.
Essential Corrosion Protection Strategies
Effective corrosion protection requires a multi-layered approach specifically designed for marine environments:
1. Protective Coatings and Treatments
Specialized coatings provide the first line of defense against salt corrosion:
- Enclosure treatments: Marine-grade clear coats for aluminum surfaces
- Electronic conformal coatings: For circuit boards and control systems
- Corrosion-inhibiting sprays: For electrical connections and exposed metal
- Sacrificial anodes: For certain engine and cooling system components
- Industrial-grade waxes: For external painted surfaces
- Dielectric grease: For all electrical connections
These protective applications should be renewed according to the coastal maintenance schedule, not merely applied once.
Recommended Products:
- CRC Heavy Duty Corrosion Inhibitor
- Boeshield T-9 Protectant
- MG Chemicals Silicone Conformal Coating
- NO-OX-ID A-Special Electrical Grease
- 3M Marine Protective Liquid Wax
2. Proper Cleaning Techniques
Regular cleaning is essential but must be done correctly to prevent additional damage:
- Fresh water rinses: Use low-pressure, clean freshwater to remove salt deposits
- Avoid high-pressure washing: Can drive salt particles deeper into seams and electrical components
- Mild detergent options: Use only pH-neutral, non-abrasive cleaners when necessary
- Complete drying: Ensure all surfaces are thoroughly dried after cleaning
- Specific timing: Clean after storm events, not just on a calendar schedule
- Targeted cleaning: Pay special attention to cooling fins, vents, and connection points
Always follow cleaning with appropriate protective treatments while surfaces are completely dry.
Cleaning Don'ts:
- Never use chlorine-based cleaners
- Avoid abrasive scrubbing tools
- Don't clean hot surfaces
- Skip household glass cleaners
- Don't leave components damp
3. Enhanced Enclosure Management
Generator enclosures require special attention in coastal environments:
- Seam sealing: Apply marine-grade silicone to enclosure seams
- Drain hole maintenance: Ensure proper drainage while preventing salt intrusion
- Ventilation filters: Add salt-filtering media to air intake vents
- Hardware replacement: Replace standard hardware with marine-grade alternatives
- Gasket inspection: Check and replace deteriorated gaskets immediately
- Moisture absorption: Consider desiccant packs during extended idle periods
Properly sealed enclosures significantly reduce internal corrosion rates.
Hardware Upgrades:
- 316 stainless steel fasteners
- Marine-grade aluminum components
- Brass/bronze alternatives when suitable
- Nylon washers for dissimilar metals
- UV-resistant synthetic components
4. Electrical System Protection
Electrical components are particularly vulnerable to salt air damage:
- Connection sealing: Apply dielectric grease to all connections
- Control panel protection: Add supplemental gaskets or seals around access points
- Wire harness coating: Apply protective spray to exposed wiring
- Terminal protection: Use terminal protectors and heat-shrink with adhesive lining
- Control board treatment: Professional application of conformal coating
- Junction box upgrades: Replace standard boxes with marine-grade versions
Electrical failure is the most common issue for coastal generators; these protective measures are essential.
Warning Signs:
- Green/white corrosion on terminals
- Discolored or brittle wire insulation
- Error codes during self-testing
- Intermittent operation issues
- Visible rust on connectors
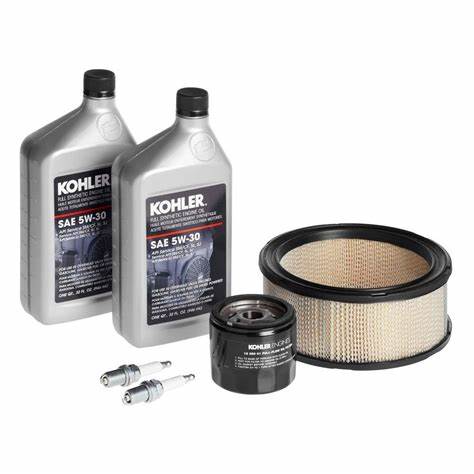
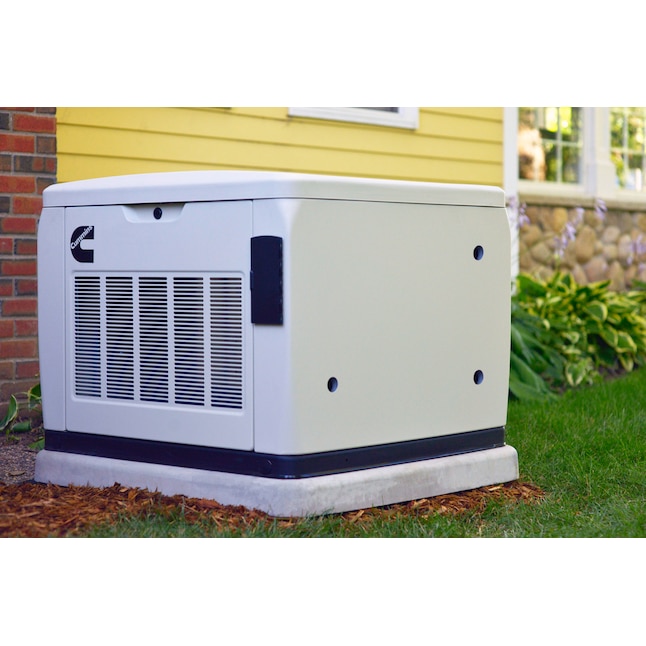
Left: Regular oil and filter changes are crucial for coastal generators. Right: A properly maintained Cummins generator with coastal-specific protection.
Case Study: Coastal Generator Lifespan Comparison
A 2023 study of 150 standby generators in Florida coastal communities revealed dramatic differences based on maintenance approaches:
- Standard maintenance schedule: 64% required major repairs or replacement within 5 years
- Enhanced coastal maintenance (partial measures): 41% required major repairs within 5 years
- Comprehensive coastal maintenance: Only 12% required major repairs within 5 years
The study found that generators receiving comprehensive coastal-specific maintenance averaged 14.3 years before requiring replacement, compared to just 6.7 years for those on standard maintenance schedules.
Source: Coastal Power Systems Reliability Study, University of Florida, 2023
Component-Specific Coastal Maintenance Procedures
Different generator systems require specific attention in coastal environments:
Engine System Protection
- Air intake filtration: Add secondary salt air filtration to prevent internal engine damage
- Oil selection: Use marine-grade oils with enhanced corrosion protection
- Crankcase ventilation: Ensure proper function to prevent internal condensation
- Cylinder protection: During extended idle periods, consider fogging oil treatment
- Exhaust system coating: Apply high-temperature corrosion-resistant coatings
- More frequent exercise: Run weekly rather than bi-weekly in coastal environments
- Oil analysis: Conduct semi-annual oil analysis to detect salt contamination
Internal engine corrosion from salt-laden intake air is a leading cause of premature coastal generator failure.
Fuel System Considerations
- Fuel tank condensation: Keep tanks full and use moisture-control additives
- Fuel line protection: Inspect for external corrosion and protect with appropriate coatings
- Filter changes: Replace fuel filters more frequently due to accelerated degradation
- Natural gas components: Provide additional protection for regulators and connections
- Propane tank placement: Consider location to minimize salt spray exposure
- Tank inspection: Check for external corrosion signs quarterly
- Water separator maintenance: Install and service fuel water separators
Fuel system corrosion can create dangerous fuel leaks and delivery problems during emergency operation.
Cooling System Maintenance
- Radiator cleaning: Gentle freshwater rinse from inside out to remove salt deposits
- Coolant selection: Use extended-life formulations with corrosion inhibitors
- Cooling fin protection: Apply thin protective coatings to external cooling fins
- Hose inspection: Check for cracking from salt exposure and UV damage
- Fan maintenance: Ensure plastic fans aren't deteriorating from salt exposure
- Water pump service: Inspect for signs of seal deterioration or shaft corrosion
- Temperature monitoring: Install additional monitoring to detect cooling efficiency loss
Cooling system efficiency significantly impacts generator performance and longevity in hot coastal climates.
Battery and Starting System Care
- Marine-grade batteries: Upgrade to batteries designed for saltwater environments
- Terminal protection: Apply terminal-specific protectants and covers
- Charging system check: Verify charging system output monthly
- Cable inspection: Look for corrosion under insulation at terminal ends
- Battery box ventilation: Ensure proper ventilation while preventing salt intrusion
- Starter motor protection: Apply protective coatings to external starter components
- Solenoid maintenance: Protect exposed solenoid terminals and connections
Starting system failure is the most common reason coastal generators fail to operate during power outages.
Coastal Generator Upgrades and Retrofits
For existing generators in coastal locations, these upgrades can significantly extend service life:
Enclosure and Housing Upgrades
- Marine-grade aluminum replacement panels for severely corroded sections
- Aftermarket sealing kits for enclosure gaps and seams
- Aftermarket sealing kits for enclosure gaps and seams
- Salt air filtration systems for enclosure ventilation
- Secondary protective enclosures for extreme coastal exposure
- Improved drainage systems to prevent water pooling
- Hardware replacement with marine-grade alternatives
- UV-resistant canopy additions for additional protection
Cost range: $300-$2,500 depending on generator size and upgrade extent
Environmental Control Systems
- Dehumidification systems for enclosure moisture control
- Positive pressure ventilation to reduce salt air infiltration
- Upgraded breather vents with improved filtration
- Climate-controlled battery compartments for extended battery life
- Saltwater detection sensors for flood-prone areas
- Improved cooling airflow management to reduce internal condensation
- Remote environmental monitoring systems
Cost range: $500-$2,500 depending on system sophistication
When evaluating these upgrades, prioritize those addressing the specific coastal challenges most relevant to your location. Proximity to open salt water, prevailing winds, and generator placement all influence which upgrades will provide the best return on investment.
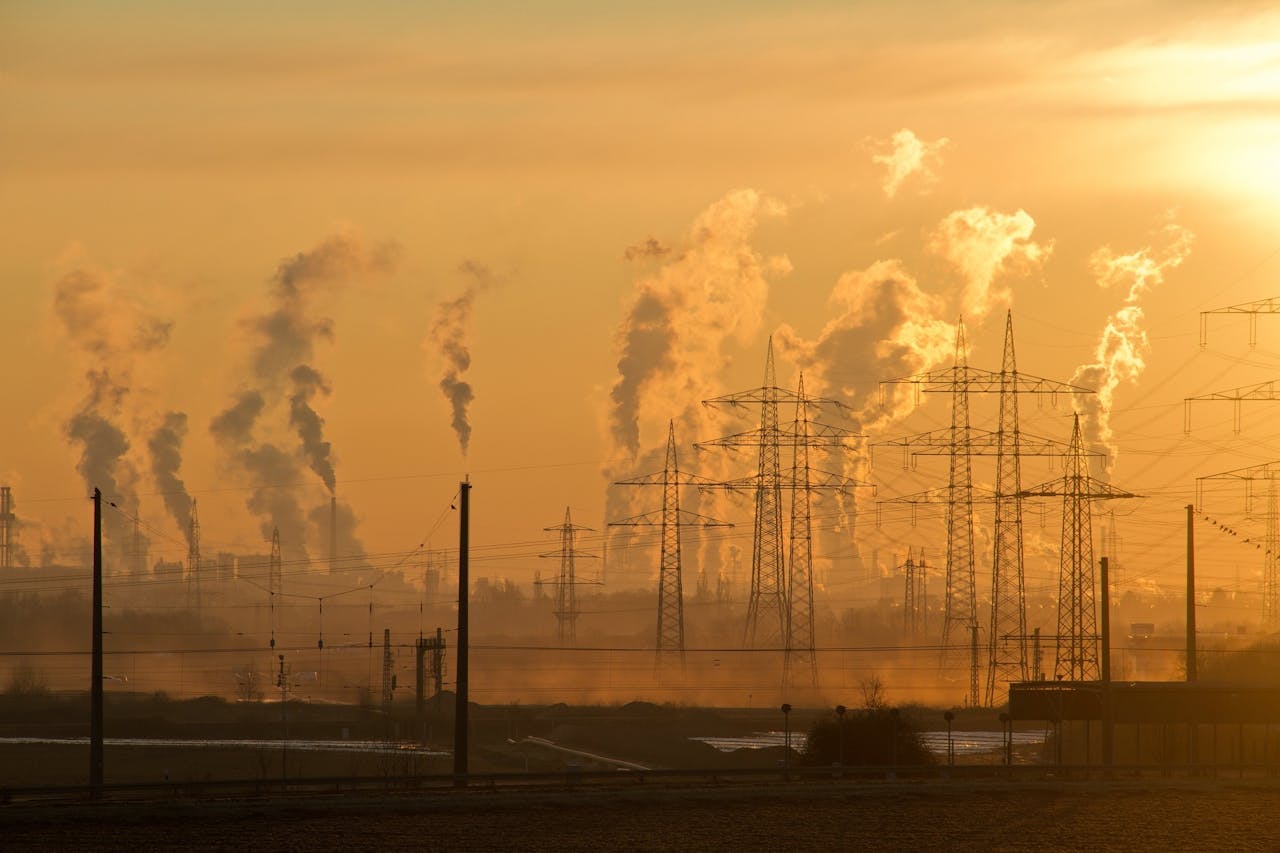
A coastal generator installation with enhanced environmental protection features, including elevated mounting and weather shielding
Selecting Coastal-Ready Generators
If you're purchasing a new generator for a coastal location, certain features and options significantly improve long-term reliability:
Feature | Standard Option | Coastal Recommendation | Benefit |
---|---|---|---|
Enclosure Material | Painted steel or aluminum | Marine-grade aluminum with advanced coatings | 3-4× longer corrosion resistance |
Hardware | Zinc-plated or stainless steel | 316 stainless steel throughout | Virtually eliminates fastener deterioration |
Cooling System | Standard radiator | Coated radiator with enhanced corrosion protection | Prevents cooling efficiency degradation |
Circuit Protection | Standard enclosures | Sealed, conformal-coated electronics | Prevents salt air infiltration to circuits |
Ventilation System | Basic intake screening | Salt-filtered air intake system | Reduces internal salt contamination |
Paint System | Standard powder coating | Marine-grade multi-stage coating | Provides enhanced barrier protection |
Connection Sealing | Standard gaskets | Enhanced gasketing and sealing system | Prevents moisture and salt penetration |
Warranty Coverage | Standard warranty | Coastal environment warranty coverage | Ensures protection for marine installations |
Several manufacturers offer specific coastal packages or marine-grade options for their standby generators. These factory-equipped units typically include multiple coastal adaptations and may offer extended warranty coverage when maintained according to coastal specifications.
Popular Generators with Marine-Grade Options
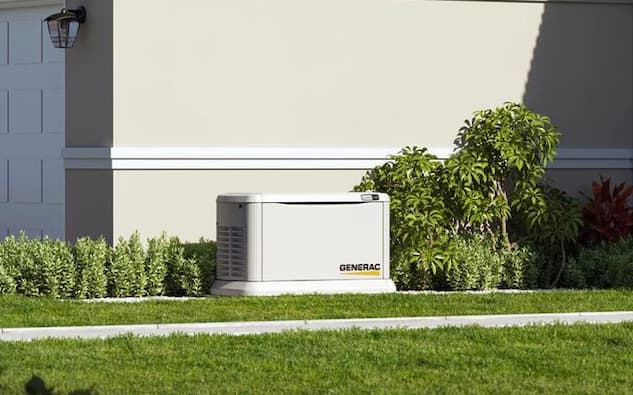
Generac with Coastal Package
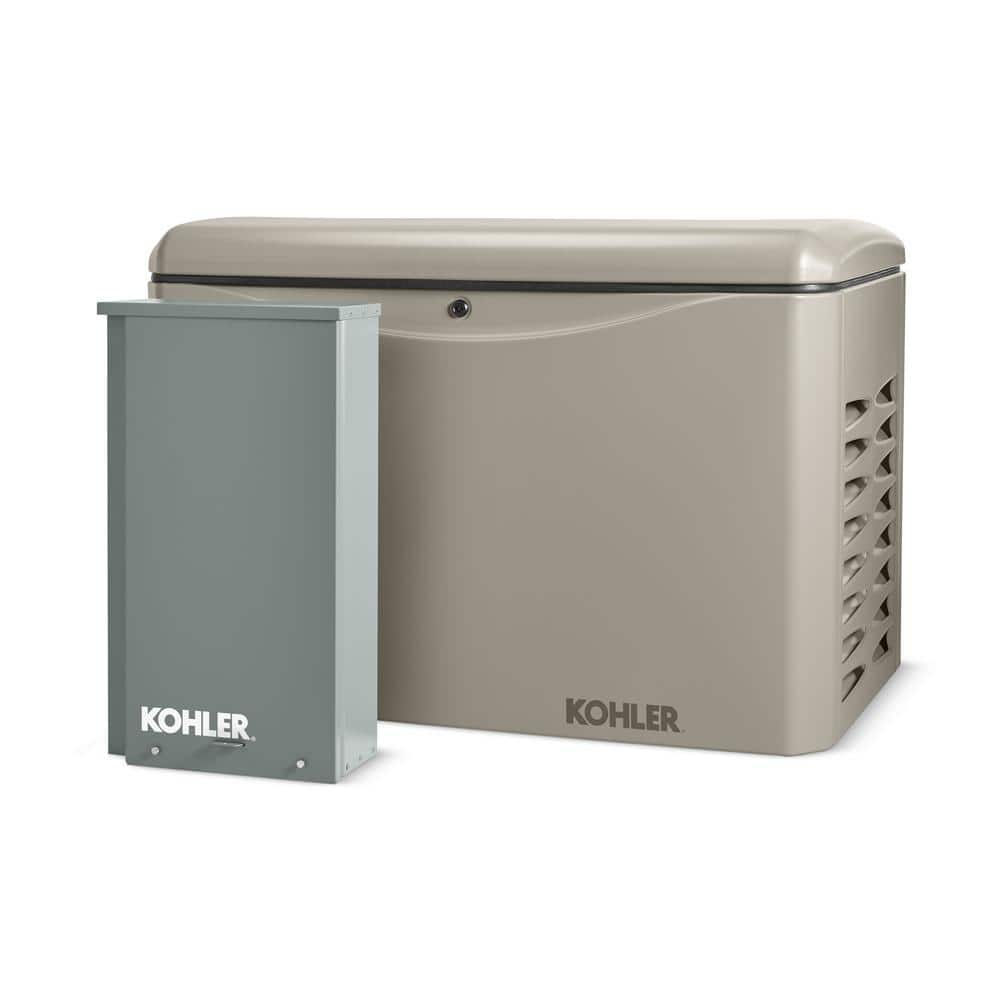
Kohler Marine-Grade
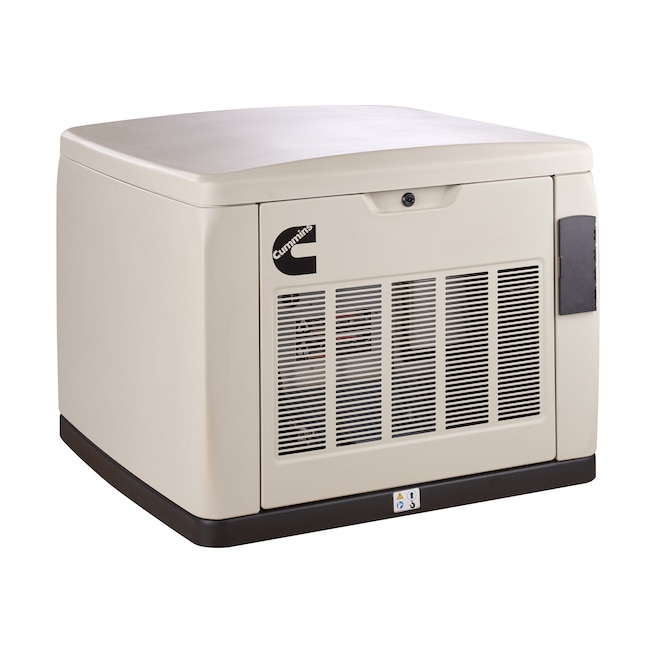
Cummins Coastal Series
Professional Maintenance Partnerships
Selecting the right service provider is particularly important for coastal generators:
Choosing a Coastal Generator Specialist
- Verify specific experience with coastal installations
- Ask about marine-grade components and procedures
- Check if they offer coastal-specific maintenance plans
- Confirm technicians have salt air corrosion training
- Request references from other coastal customers
- Ensure they stock specialized materials and coatings
- Verify availability during hurricane season/storm events
Service Contract Considerations
- Look for contracts with coastal-specific inspection points
- Ensure accelerated service schedule appropriate for salt exposure
- Verify coverage for corrosion-specific issues
- Consider contracts including protective coatings renewal
- Check if post-storm inspections are included
- Confirm whether marine-grade replacement parts are used
- Ask about remote monitoring options for corrosion conditions
Questions to Ask Potential Service Providers
- What specific measures do you take for generators in saltwater environments that differ from standard service?
Look for detailed answers about specific procedures, not general reassurances
- Do you apply protective coatings as part of your service, and if so, what products do you use?
They should name specific marine-grade products appropriate for generators
- How do you protect electrical connections and control systems from salt corrosion?
Listen for mentions of dielectric grease, conformal coatings, and connection sealing
- What is your recommended service interval for coastal generators, and why?
Should recommend more frequent service than standard inland intervals
- Can you provide references from other customers with generators in similar coastal exposure?
Contact these references to ask about long-term satisfaction
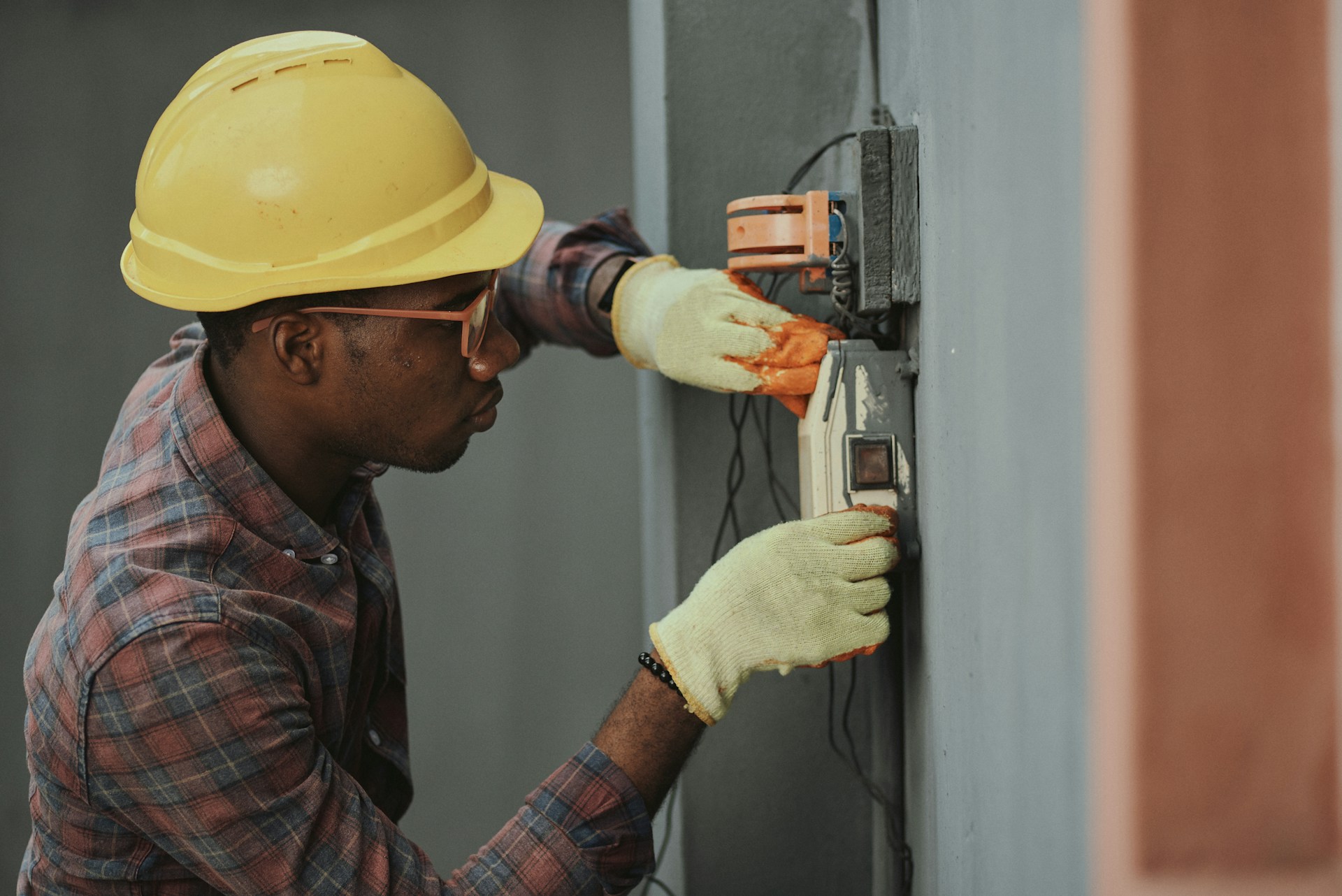
A certified technician applying specialized protective coatings to electrical components in a coastal generator
Common Questions About Coastal Generator Maintenance
How far inland do special coastal maintenance practices need to be followed?
The need for coastal maintenance protocols diminishes with distance from saltwater, but doesn't follow a simple mileage rule. Several factors determine salt exposure inland: (1) Prevailing wind patterns that can carry salt spray much further in certain directions; (2) Elevation, with higher locations often experiencing more salt air exposure; (3) Natural barriers like dense vegetation or hills that may provide some protection; and (4) Local microclimates affecting salt distribution. As a general guideline, properties within 1 mile of saltwater should definitely follow full coastal protocols. Properties 1-10 miles inland should follow modified coastal maintenance depending on local conditions. Even locations 10-15 miles inland may benefit from selected coastal practices in areas with strong onshore winds. A good test is to place a clean glass surface outdoors for several days, then check for a salt film when dried—if visible salt accumulates, coastal maintenance procedures are warranted.
Is it worth maintaining an older generator in a coastal environment, or should I replace it?
For generators more than 10 years old in coastal environments, the replacement-versus-maintenance decision should consider several factors: (1) Current condition—if significant corrosion already exists in critical components or the engine itself, replacement is often more cost-effective; (2) Parts availability—some older models have limited availability of replacement components; (3) Upgrade options—newer models offer significantly improved corrosion resistance and coastal features; (4) Efficiency and reliability improvements in newer models; and (5) The total investment needed for comprehensive coastal retrofitting. As a rule of thumb, if restoring an older generator to proper coastal condition would cost more than 40-50% of a new coastal-ready replacement, upgrading to a new unit typically offers better long-term value. However, if the existing generator is structurally sound with mainly surface corrosion, a refurbishment program using the techniques outlined in this guide can often extend service life by 5-7 additional years.
What are the best practices for seasonal coastal properties?
Seasonal properties present unique challenges as generators often sit idle for extended periods in corrosive environments. For optimal protection: (1) Invest in comprehensive pre-season and post-season service visits scheduled just before arrival and after departure; (2) Install remote monitoring systems that alert you to potential issues while away; (3) Apply specialized long-term storage products before departure, including engine fogging oil and enhanced corrosion protectants; (4) Arrange for monthly brief exercise cycles with a local service provider; (5) Consider engine dehumidification systems that maintain a controlled environment within the generator; (6) Use waterproof but breathable generator covers specifically designed for marine environments; and (7) Install humidity indicators visible through covers to monitor conditions remotely via caretakers. Additionally, maintaining climate control in adjacent structures even at minimal levels can significantly reduce condensation cycles that accelerate corrosion.
Protect Your Coastal Generator Investment
Proper maintenance is essential for ensuring your standby generator performs reliably in challenging coastal environments.
Related Articles
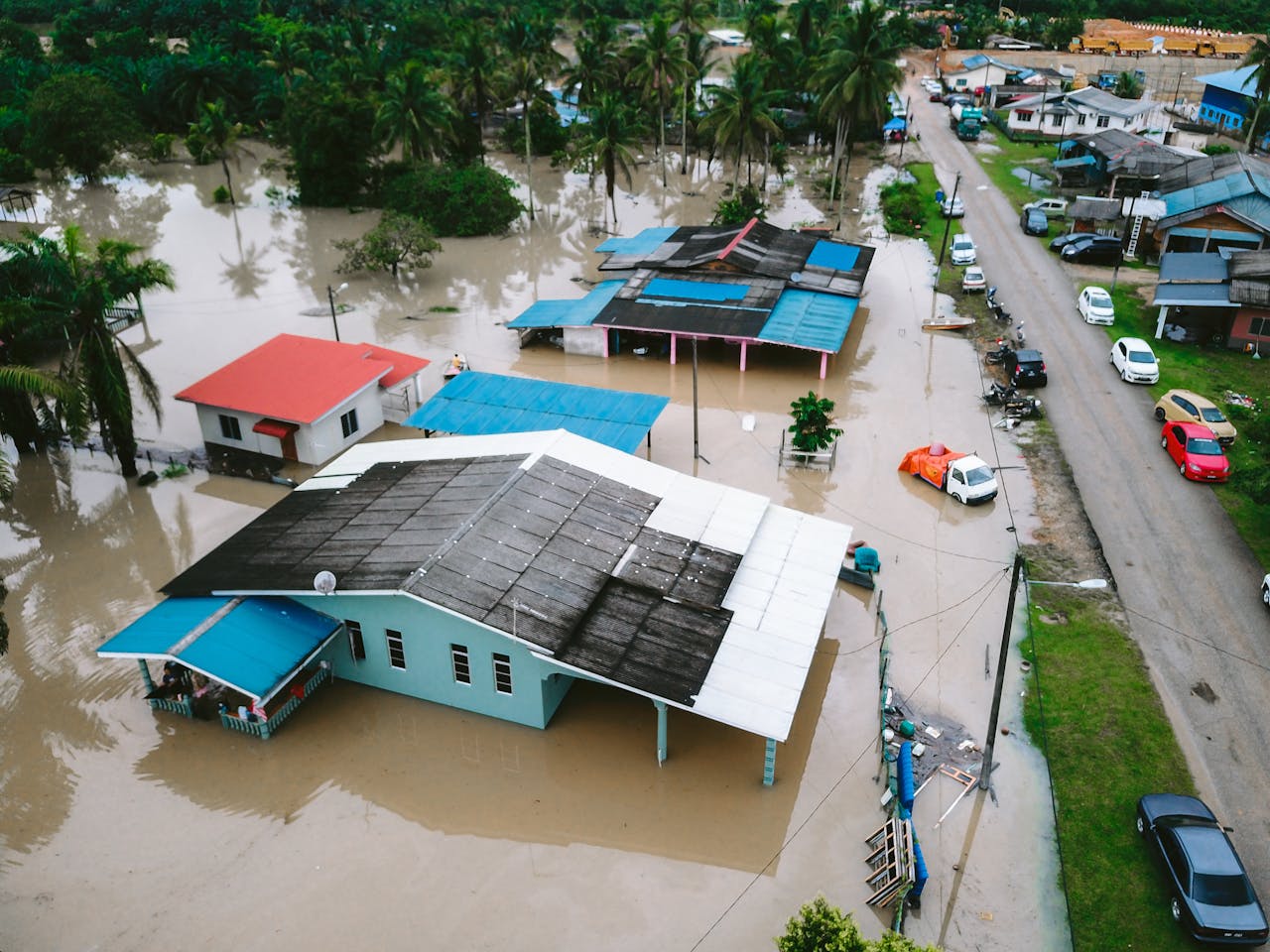
Best Standby Generator Placement for Homes in Flood-Prone Areas
Learn optimal generator placement strategies for coastal areas subject to flooding.
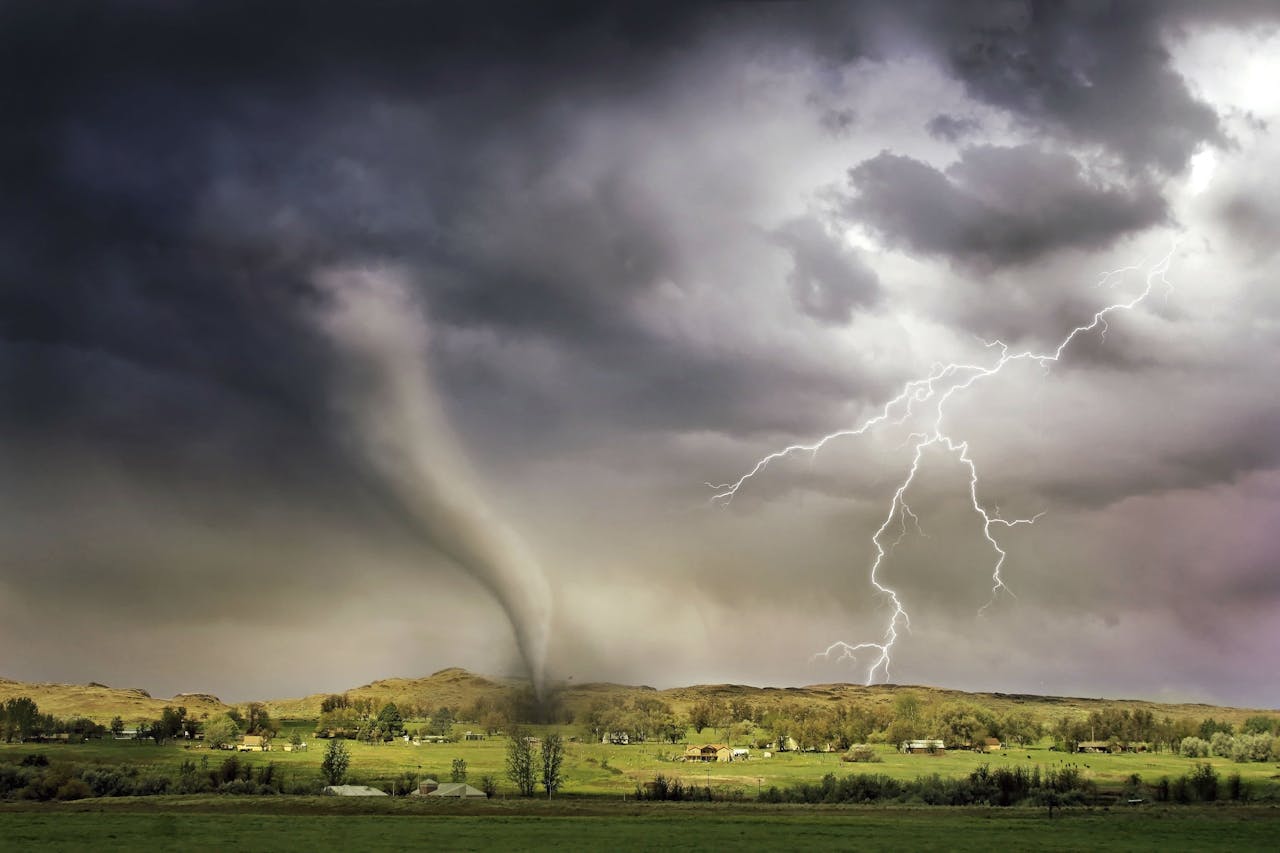
Extreme Weather Generator Operation
Discover how to prepare your generator for hurricane season and other coastal weather events.
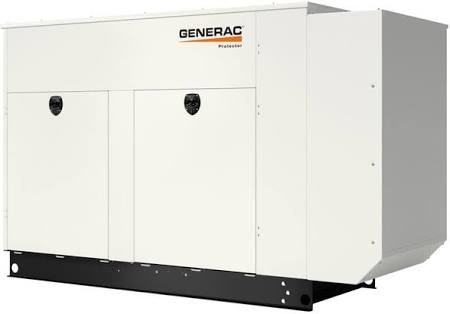
Top 5 Home Standby Generators for 2025
Compare the latest generators including their suitability for coastal environments.
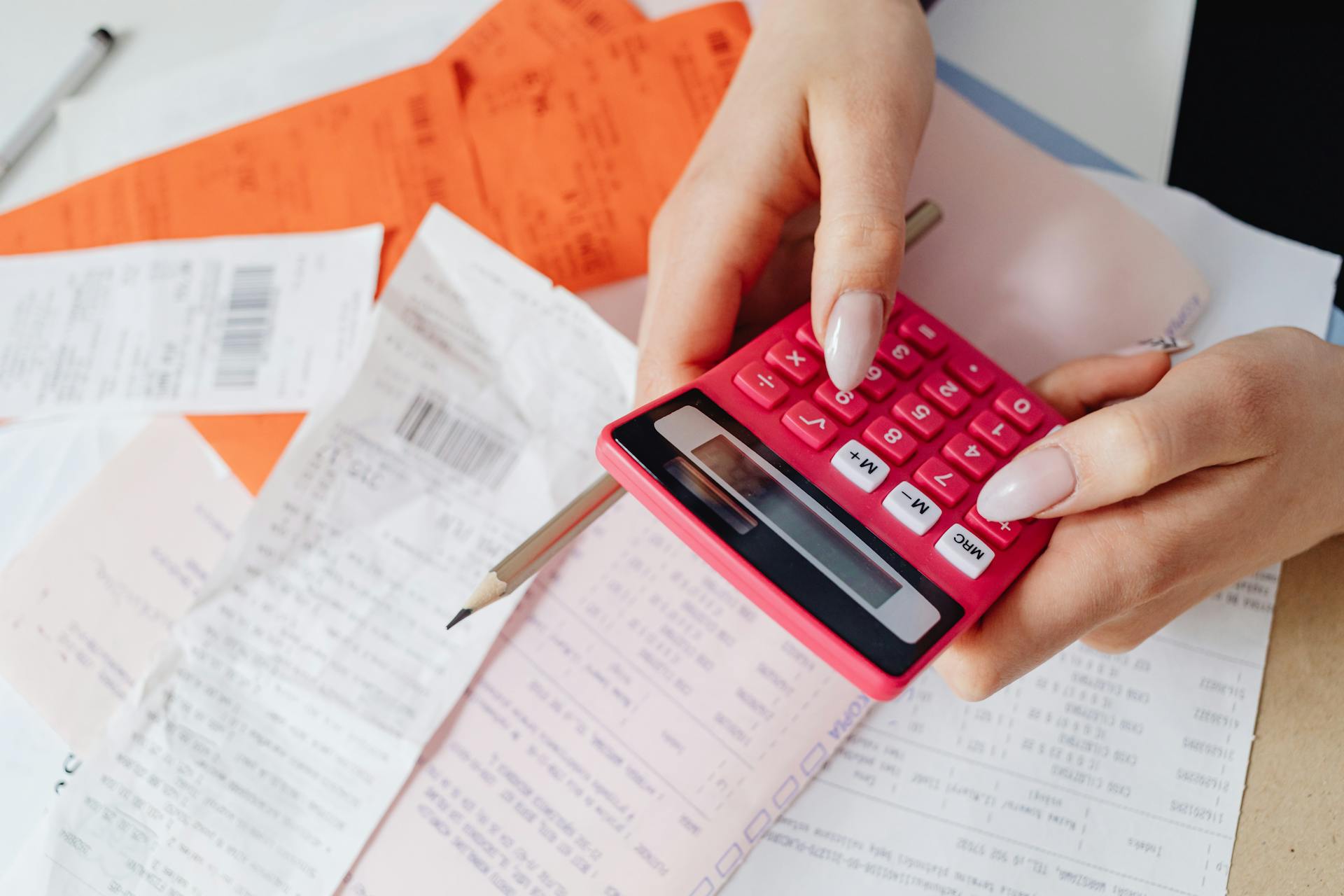
The Hidden Costs of Owning a Standby Generator
Understand the financial implications of coastal generator maintenance requirements.
Key Takeaways
- Coastal environments accelerate generator deterioration by 3× or more without proper maintenance
- Maintenance intervals should be at least twice as frequent as standard inland recommendations
- Specialized protective coatings and treatments are essential for salt air protection
- Electrical connections require specific protection to prevent salt-induced corrosion
- Upgrade options like marine-grade components can significantly extend coastal generator lifespan
- Professional maintenance partners with coastal experience provide superior protection
- Generator choice matters—select models with factory coastal protection packages when possible
- The investment in proper coastal maintenance typically pays for itself many times over through extended generator life and reliability